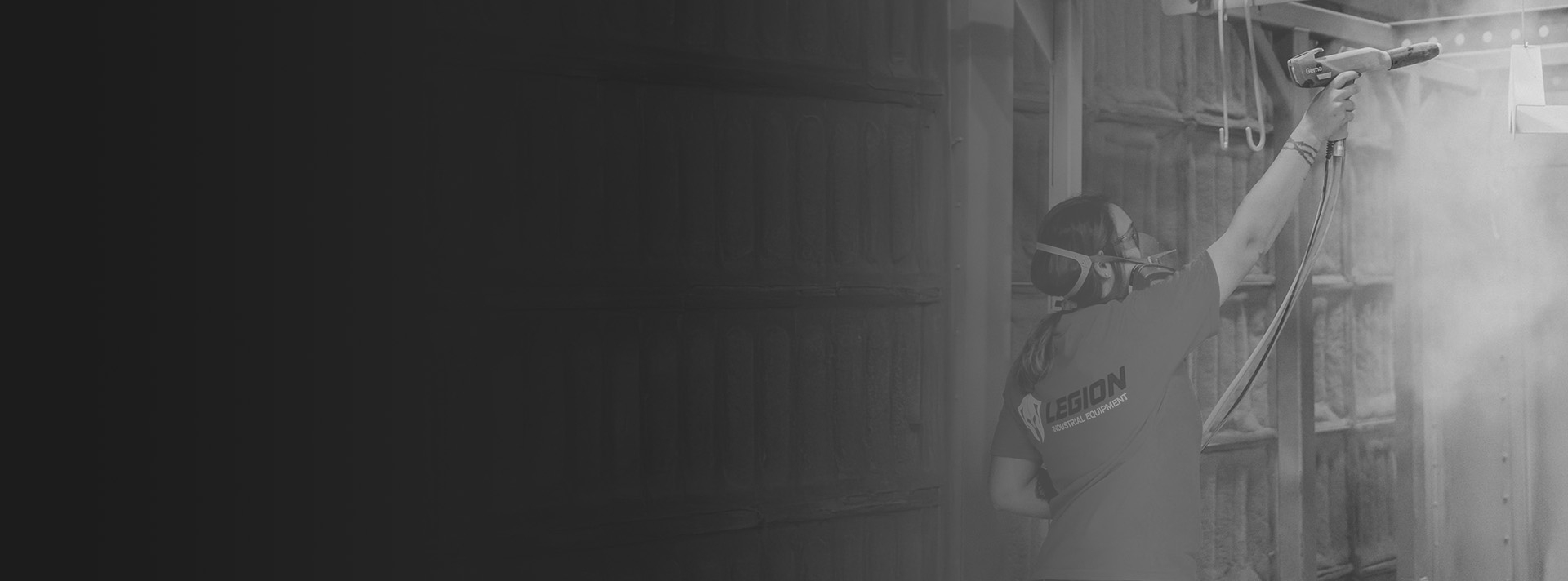
Start-to-Finish
We specialize in start-to-finish projects, managing every aspect of the process to deliver complete, high-quality solutions for our clients.
Success In
START-TO-FINISH PROJECTS
With expertise in start-to-finish projects, we manage every aspect of the process to deliver complete, high-quality solutions for our clients.
Follow Legion’s steps to success in these project examples:
OEM Product Manufacturing for an Automotive Company
Start
The project begins with a collaboration between our design and engineering teams and the customer’s technical experts to fully understand the part’s requirements. We receive detailed CAD models and prints to create prototypes that ensure the design meets all functional and quality standards.
Fabrication & Assembly
Once the first article is approved, we move into full-scale production, using advanced CNC machines and precision welding to fabricate the part. This includes rigorous quality control processes to ensure each part meets exact specifications.
Finishing
After fabrication, we apply the necessary surface finishes, such as powder coating or protective treatments, to enhance durability and aesthetics.
Delivery
We handle the logistics of transporting the completed parts to the automotive company, ensuring they are delivered on time and ready to be installed on their vehicles.
End Result
The customer receives a fully built, OEM-ready part that integrates seamlessly into their final product, delivered on schedule to meet production demands.
Custom-Made Production Line Equipment for a Raw Steel Processing Plant
Start
The steel processing plant requires specialized equipment to streamline their production line. Our team works closely with them to design custom machinery that optimizes workflow, increases efficiency, and meets the unique challenges of their operation.
Fabrication
Using precision metal fabrication techniques, we manufacture the equipment, which could include conveyors, automated systems, or material handling components. Each piece is built to withstand the rigors of the steel processing environment.
Finishing
The equipment is finished with protective coatings to ensure durability and resistance to wear, heat, and corrosion typical in raw steel processing environments.
Installation & Testing
Once the equipment is fabricated, we transport it to the client’s facility, install it, and perform on-site testing to ensure it functions as expected within their existing systems.
End Result
The customer receives fully customized, high-performance production line equipment that improves their operational efficiency and production capacity.
Custom Facilities Support Equipment for a Chemical Processing Plant
Start
The client requires customized facilities support equipment, such as mezzanines, material handling solutions, racks, and carts, to improve the efficiency and safety of their plant. We collaborate with their engineering team to design tailored solutions that meet their specific operational needs.
Fabrication & Assembly
We manufacture the equipment using high-quality materials to ensure safety and compliance with industry standards. This includes structural supports like mezzanines and material handling systems designed for chemical processing environments.
Installation
After fabrication, our team installs the equipment on-site, ensuring that everything is properly set up, integrated into the facility, and ready for use.
End Result
The customer receives a suite of custom-designed facilities support equipment, fully installed and operational, enhancing their plant’s efficiency and safety standards.
Discover more with Legion.
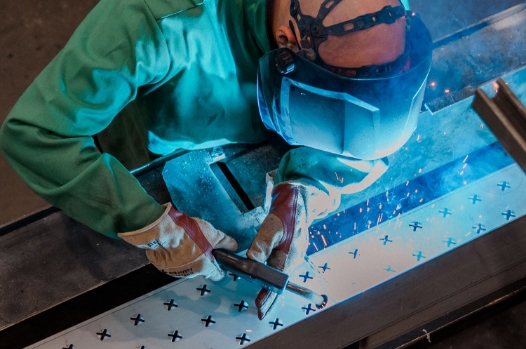

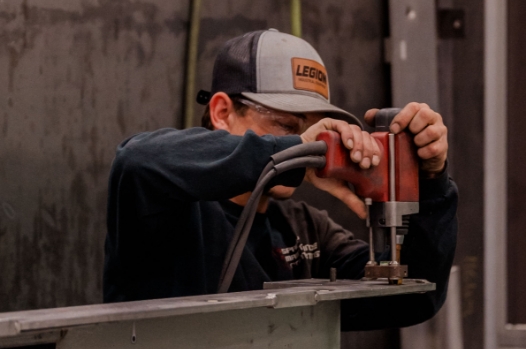
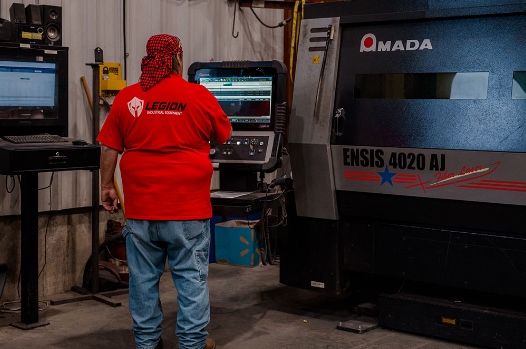
These examples illustrate Legion’s ability to manage complex, start-to-finish projects, to deliver custom solutions across a variety of industries. Our full-service approach ensures that every aspect of the project is handled with precision, from design to installation.
Contact Us
Contact one of our representatives today to get started on your next project or join the Legion team by applying for one of our available positions.